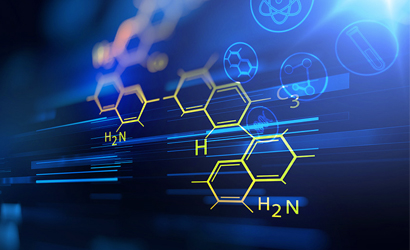
提釩固廢硫酸鈉生產(chǎn)硫化鈉的方法

硫化鈉又稱臭堿、臭蘇打、黃堿、硫化堿。硫化鈉為無(wú)機(jī)化合物,純硫化鈉為無(wú)色結(jié)晶粉末。吸潮性強(qiáng),易溶于水。水溶液呈強(qiáng)堿性反應(yīng)。觸及皮膚和毛發(fā)時(shí)會(huì)造成灼傷。故硫化鈉俗稱硫化堿。硫化鈉水溶液在空氣中會(huì)緩慢地氧化成硫代硫酸鈉、亞硫酸鈉、硫酸鈉和多硫化鈉。
現(xiàn)有的硫化鈉的生產(chǎn)方法主要有煤粉還原法、吸收法、硫化鋇法和氣體還原法等,而煤粉還原法在工業(yè)生產(chǎn)中使用較多。煤粉還原法是將芒硝與煤粉按照配比在高溫下混合煅燒還原,經(jīng)過(guò)后
續(xù)處理得到硫化鈉產(chǎn)品。然而,其采用的原料的純度要求較高,成本較高,同時(shí)在生產(chǎn)的過(guò)程中煤粉消耗量大,產(chǎn)生的廢渣較多,不利于環(huán)保。
本技術(shù)的目的在于解決現(xiàn)有技術(shù)中存在的技術(shù)問(wèn)題,提供一種成本低,能源利用率高,產(chǎn)生的廢棄物少,安全環(huán)保的基于提釩固廢硫酸鈉生產(chǎn)硫化鈉的方法。
二:操作方法
①:配料:稱取固廢硫酸鈉、焦粉和硫化鋇放入轉(zhuǎn)爐中;
②:焙燒:對(duì)①所述的轉(zhuǎn)爐加熱,進(jìn)行焙燒反應(yīng),生成堿渣和熔融狀硫化鈉;
③:熱化浸?。簩ⅱ谒龅娜廴跔盍蚧c轉(zhuǎn)入熱水中攪拌浸取,得到粗渣和一級(jí)硫化 鈉水溶液;
④:除渣澄清:對(duì)步驟③所述的一級(jí)硫化鈉水溶液靜置,固液分離操作后,得到細(xì)渣和二 級(jí)硫化鈉水溶液;
⑤:蒸發(fā)濃縮:將步驟④所述的二級(jí)硫化鈉水溶液,蒸發(fā)濃縮,得到濃縮后的硫化鈉水溶 液。
⑥結(jié)晶:將步驟⑤得到的濃縮后的硫化鈉溶液冷卻 結(jié)晶,得到固體硫化鈉。
三:有益效果
本技術(shù)的基于固廢硫酸鈉生產(chǎn)硫化鈉的方法采用提釩工藝產(chǎn)生的固廢硫酸鈉作為原料將廢料二次使用,降低了原料成本;采用焦粉作為還原劑,采用焦粉替代傳統(tǒng)生產(chǎn)工藝中的煤粉作為還原劑減少了原料消耗,焦粉中固定碳含量比煤粉高10%左右能大幅提升還原率,減少還原劑用量,從而減少本方法最終的固廢量;焦粉揮發(fā)度僅2%,從而使煙氣排放比采用無(wú)煙煤減少6%,所采用焦粉可以為焦化廠副產(chǎn)物,屬于二次資源,更環(huán)保;采用硫化鋇作為沉淀劑,可以將生產(chǎn)原料中含有的氫氧化鈉、碳酸鈉、硫代硫酸鈉和亞硫酸鈉,更有效地轉(zhuǎn)化為硫化鈉,從而提高使得本方法在最大限度的提升硫化鈉的生產(chǎn)率的同時(shí)將原料的多余的雜質(zhì)除去;
本技術(shù)的基于固廢硫酸鈉生產(chǎn)硫化鈉的方法采用將方法生產(chǎn)過(guò)程中產(chǎn)生的粗渣處理后,用作加熱轉(zhuǎn)爐的原料或者其它的原料使用從而節(jié)省了能源消耗,提升了能源利用率;提供將細(xì)渣多次洗滌處理后排放,較少了對(duì)環(huán)境的污染,將洗滌后的溶液進(jìn)行回用,提高了能源利用率,減少了對(duì)環(huán)境的污染,使本技術(shù)更安全環(huán)保;
本技術(shù)的基于固廢硫酸鈉生產(chǎn)硫化鈉的方法采用配料、焙燒、熱化浸取、除渣澄清、蒸發(fā)濃縮和結(jié)晶的生產(chǎn)工藝流程,優(yōu)化生產(chǎn)工藝使得產(chǎn)生的固廢更少,生產(chǎn)成本更低,對(duì)環(huán)境更友好,從而使本技術(shù)產(chǎn)生更好的經(jīng)濟(jì)效益和環(huán)保效益。
*免責(zé)聲明:本網(wǎng)站所載內(nèi)容來(lái)源于互聯(lián)網(wǎng)、微信公眾號(hào)等公共渠道,我們對(duì)文中觀點(diǎn)保持中立態(tài)度。本文資訊僅供參考,交流之用。本網(wǎng)站不對(duì)任何因使用所載內(nèi)容所引致的損失承擔(dān)任何風(fēng)險(xiǎn)及責(zé)任。轉(zhuǎn)載的稿件版權(quán)歸原著所有,如有侵權(quán),請(qǐng)聯(lián)系我們刪除。